Selecting the right drum handling equipment for your business in 2025 involves a careful assessment of various factors. First, understanding the types and sizes of drums you deal with is crucial, along with how often they’re handled. For low-volume operations, manual tools like dollies might suffice, but high-volume needs may call for powered options. Safety features cannot be overlooked; equipment should have guards and meet OSHA standards to protect workers. Think about durability—corrosion-resistant materials are important if you’re handling hazardous substances. Lastly, evaluate suppliers and see if you can test their equipment before buying; it ensures a good match for your specific environment.
1. Understand Your Drum Handling Needs
To select the best drum handling equipment, start by understanding the specific needs of your operations. First, assess the types of drums you handle. Are they plastic, metal, or do they contain hazardous materials? Each type may require different handling solutions. Next, determine the weight and size of the drums. Heavier and larger drums will necessitate more robust equipment. Additionally, consider how often you handle these drums and the environment in which these operations occur—whether it’s indoors, outdoors, or in wet and dry conditions. This understanding will lay the groundwork for identifying the most suitable equipment for your business.
2. Types of Drum Handling Equipment
When it comes to drum handling equipment, understanding the different types available is crucial for making the right choice for your business. Manual handling equipment, such as drum dollies and manual drum lifters, is ideal for low-volume operations where flexibility and lower costs are priorities. For businesses that deal with higher volumes or heavier drums, powered equipment like electric drum handlers and forklifts can save time and reduce labor intensity. Specialized equipment, such as drum tippers and drum rollators, caters to specific needs, like pouring or transporting drums in tight spaces. Each type has its own advantages and fits different operational scenarios, so evaluating what works best for your specific tasks is essential.
3. Essential Safety Features to Consider
When selecting drum handling equipment, prioritizing safety features is crucial to protect your employees and comply with regulations. Look for equipment with safety guards that prevent accidental injury during operation. Automatic shut-off features can add an extra layer of safety by stopping the equipment if it detects a malfunction or an unsafe condition. Ergonomic designs are also vital, as they help reduce the risk of strain and injury for operators who regularly handle heavy drums.
Moreover, ensure that the equipment meets OSHA regulations and other relevant safety standards. This compliance not only protects workers but also shields your business from potential legal issues. Stability is another essential factor; choose equipment that offers robust control mechanisms to prevent tipping or slipping, especially when handling hazardous materials. For instance, drum tippers with secure locking systems can significantly enhance safety during the tipping process.
- Automatic shut-off mechanisms
- Emergency stop buttons
- Safety guards and barriers
- Load limit indicators
- Ergonomically designed handles
- Slip-resistant bases
- Visible warning signals
4. Material Quality and Durability
When selecting drum handling equipment, the material quality and durability are critical factors. Opt for equipment made from robust materials like heavy-duty steel or high-quality polymers designed to endure the rigors of daily use. For instance, if your operations involve handling corrosive or hazardous materials, consider equipment with corrosion-resistant coatings. This ensures longevity and reduces the risk of equipment failure due to environmental factors. Furthermore, check the load capacity ratings to ensure that the equipment can handle the weight of the drums you intend to move. Investing in high-quality, durable equipment not only enhances safety but also minimizes maintenance costs over time.
5. User-Friendliness of Equipment
When selecting drum handling equipment, user-friendliness plays a crucial role in ensuring smooth operations. It’s essential to choose equipment that operators can understand and use with minimal training. Look for intuitive controls and clear instructions that allow new users to quickly get up to speed. For instance, powered drum handlers with simple joystick controls can significantly reduce the learning curve compared to more complex machinery.
Adjustable components are another aspect to consider; equipment that can easily accommodate different drum sizes and weights will streamline processes and minimize downtime. For example, a drum lifter with adjustable forks can handle various drum types without requiring constant readjustment, making it more versatile.
Additionally, ease of maintenance is vital. Equipment that allows for straightforward repairs and upkeep can save time and reduce operational disruptions. For example, a drum dolly with removable wheels can be serviced quickly, ensuring that the equipment remains in optimal working condition. In essence, prioritizing user-friendliness in drum handling equipment not only enhances productivity but also contributes to a safer and more efficient workplace.
6. Budgeting for Drum Handling Equipment
When budgeting for drum handling equipment, it’s essential to consider more than just the initial purchase price. Analyze the total cost of ownership, including maintenance and training expenses. For example, an electric drum handler may have a higher upfront cost but could save you money in the long run by reducing labor costs and increasing efficiency. Also, factor in potential repairs and the lifespan of the equipment. Investing in high-quality, durable equipment might seem expensive initially, but it often pays off through lower maintenance needs and longer service life. Don’t forget to include any required accessories or safety gear in your budget. This comprehensive approach ensures you’re prepared for both immediate and future expenditures.
7. Evaluating Supplier Reputation
Choosing the right supplier for your drum handling equipment is crucial for ensuring reliability and performance. Start by researching potential suppliers to gauge their reputation in the industry. Look for companies that have a track record of delivering quality products and excellent customer service. Reading customer reviews can provide valuable insights into their reliability and responsiveness. Additionally, consider suppliers that offer comprehensive warranty options, as this indicates their confidence in the durability of their products. For instance, a supplier with numerous positive case studies demonstrating their equipment’s effectiveness in real-world applications is often a safer choice. Engaging with industry forums and networks can also help you uncover experiences from other businesses, allowing you to make a more informed decision.
8. Planning for Future Equipment Needs
When selecting drum handling equipment, it’s crucial to think ahead. The needs of your business can change due to various factors, such as increased production volume or the introduction of new drum types. Consider equipment that offers flexibility and adaptability. For instance, modular systems allow you to expand or upgrade your setup as your demands grow, rather than needing to invest in entirely new equipment.
Another aspect to consider is the technological advancements in drum handling. In 2025, you might find equipment that integrates with automation systems or offers remote monitoring capabilities. Choosing equipment that embraces these innovations can lead to greater efficiency in your operations.
Moreover, think about the potential for shifts in regulatory requirements. Selecting equipment that can easily comply with future safety or environmental standards can save your business time and money in the long run. For example, if your business moves towards more eco-friendly practices, having equipment that supports this transition can be a significant advantage.
9. Importance of Equipment Trials
Testing drum handling equipment before making a purchase is crucial. Organizing a trial allows you to see how the equipment performs in your specific working environment. For instance, if you handle heavy metal drums, a demonstration can showcase if the electric drum handler can manage the weight efficiently without straining. Feedback from your operators during these trials is invaluable. They can provide insights on usability and comfort, ensuring that the chosen equipment aligns with their practical needs. This hands-on experience can prevent costly mistakes, ensuring that the equipment not only meets your operational demands but also enhances safety and efficiency in your workflow.
10. Training and Support for Operators
Providing thorough training for operators is essential to ensure they can use drum handling equipment effectively and safely. Training should cover the proper operation of the machinery, safety protocols, and emergency procedures. For instance, operators should learn how to secure drums properly to prevent accidents during transport. Additionally, ongoing support from the supplier is crucial. Access to technical assistance, maintenance guidance, and troubleshooting resources can significantly reduce downtime and enhance productivity. Suppliers that offer comprehensive training programs and responsive support channels demonstrate their commitment to customer success, making them a valuable partner for your business.
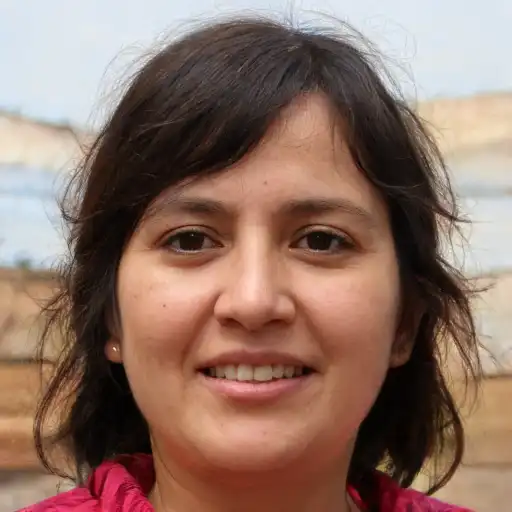
Mary Burns is a dedicated writer focusing on health and fitness topics. With a passion for promoting wellness and vitality, Mary shares her knowledge and expertise through engaging and informative blog posts.