When managing a facility that deals with heavy materials, liquids, or chemicals, ensuring the safe and efficient handling of drums is essential. Whether you’re in a manufacturing plant, warehouse, or distribution center, having the proper drum handling equipment can make a significant difference in productivity, safety, and overall operational efficiency.
Drum handling equipment is designed to assist in moving, lifting, storing, and securing drums of varying sizes and contents. However, choosing the right equipment for your facility depends on a variety of factors, such as the type of drums you’re handling, the contents, the environment, and the specific tasks at hand. In this guide, we’ll cover important considerations when selecting drum handling equipment to ensure you make an informed decision that meets your facility’s needs.
Types of Drum Handling Equipment
Before diving into the selection process, it’s important to understand the types of drum handling equipment available. Here are some common types:
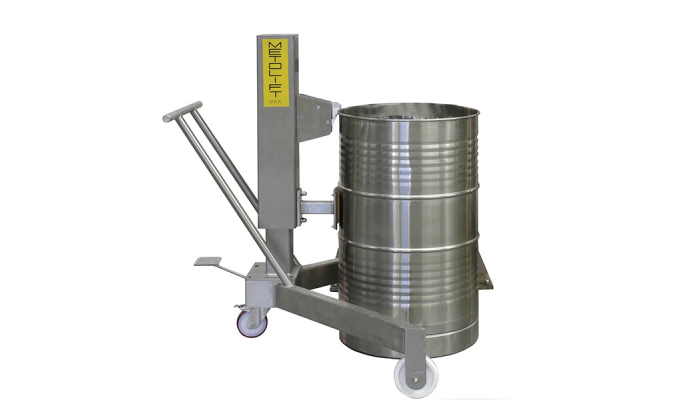
- Drum Lifts: These devices are used to lift and place drums onto pallets, shelves, or other surfaces. Drum lifts can be manual, electric, or pneumatic, depending on the weight and frequency of drum handling.
- Drum Rollers: These are used to move drums from one place to another by rolling them along a track. Drum rollers are often used in production lines where the goal is to move drums with minimal effort.
- Drum Tilters: These machines tilt drums to empty their contents or to ensure they are properly stored. Tilters are essential for operations where fluids or powders need to be dispensed from the drum.
- Drum Palletizers: This equipment is used to stack drums on top of one another on pallets, saving space and increasing the efficiency of storage.
- Drum Trucks: These are manual or powered carts designed to transport drums over short distances. They are often used for maneuvering drums in tight spaces or to deliver them to a specific area.
- Forklift Attachments: For larger facilities, forklift attachments are often used for moving drums in conjunction with the forklift. These attachments can clamp, lift, or rotate drums, making them versatile tools for handling various drum sizes.
Each type of drum handling equipment is tailored for a specific task, so understanding your operational needs will help you choose the best option.
Factors to Consider When Choosing Drum Handling Equipment
Selecting the right drum handling equipment isn’t a one-size-fits-all solution. Several factors come into play when determining which equipment will best suit your facility’s needs:
Drum Size and Weight
Drums come in different sizes, from small 15-gallon drums to large 55-gallon barrels. Additionally, some drums may be heavier than others due to the contents inside (e.g., oil, chemicals, or food-grade materials). It is essential to choose equipment that can handle the specific weight and size of the drums you need to move. Equipment with adjustable settings can accommodate a range of drum sizes, but it’s critical to ensure the capacity of the equipment is sufficient for the heaviest drums in your inventory.
Material of the Drum
The material of the drum can affect the handling process. Drums are commonly made of steel, plastic, or fiber, and each material has its own handling requirements. For instance, steel drums may require heavier-duty equipment compared to plastic ones due to their additional weight and sturdiness. Additionally, some drums may have smooth exteriors, making it more challenging to secure them. It’s important to assess the type of material you’re handling to ensure the equipment is compatible.
Contents of the Drum
The contents inside the drum play a significant role in the equipment selection. If you’re handling hazardous materials, you’ll need equipment that offers additional safety features, such as spill containment or anti-static properties. Drum handling equipment for hazardous materials must comply with safety standards and regulations to prevent accidents and ensure safe operation. On the other hand, handling food-grade or pharmaceutical products may require equipment that ensures cleanliness and contamination control.
Work Environment
The environment in which the equipment will be used is another critical factor. If your facility operates in a clean room, pharmaceutical lab, or food processing plant, you may require equipment with easy-to-clean surfaces or rust-resistant features. Additionally, if your facility is exposed to high temperatures, humidity, or extreme cold, it’s important to choose equipment designed to withstand these conditions without deteriorating or causing operational problems.
Frequency of Use
If your facility handles drums frequently, you may need drum handling equipment that is durable, efficient, and designed for high-frequency use. Electric or pneumatic equipment is ideal for frequent drum movements, as they reduce manual labor and increase productivity. On the other hand, if drum handling is less frequent, manual or semi-automatic equipment may suffice, offering a more cost-effective solution.
Available Space
The available space in your facility plays a major role in determining which equipment is best suited for your needs. If you have limited space, you may want to opt for compact equipment like drum trolleys or smaller, manual lifts. In contrast, larger facilities with ample space might benefit from more advanced options, such as drum palletizers or forklift attachments, to handle multiple drums at once.
Features to Look for in Drum Handling Equipment
When selecting drum handling equipment, there are several key features to consider:
- Ergonomics: Ensuring the safety and comfort of your workers is crucial. Ergonomically designed equipment reduces strain on workers’ bodies and helps prevent injury.
- Safety Features: For handling hazardous materials, look for equipment with safety features such as spill containment trays, non-slip grips, and protective barriers.
- Ease of Use: Drum handling equipment should be easy for operators to use and maneuver, reducing the time and effort involved in moving drums.
- Durability: Choose equipment that can withstand harsh environments, frequent use, and exposure to chemicals or extreme temperatures.
- Versatility: Some equipment is designed to handle a variety of drum sizes and materials, providing more flexibility for your facility.
Cost Considerations
While it’s important to prioritize safety and efficiency, cost is always a factor in any equipment purchase. Drum handling equipment can range in price depending on the type, capacity, and features. Be sure to evaluate your budget and weigh it against the long-term benefits of the equipment. Although it may be tempting to opt for cheaper solutions, investing in high-quality, durable equipment can save money in the long run by reducing maintenance costs and downtime.
Conclusion
Choosing the right drum handling equipment for your facility is crucial for maintaining safety, efficiency, and productivity. Understanding the types of equipment available, considering the specific needs of your operations, and evaluating key factors like drum size, weight, contents, and environment will help ensure you select the best equipment for the job. By investing in the right equipment, you can improve workflow, reduce manual labor, and create a safer workplace for your employees.
Take your time in selecting drum handling equipment, and consult with experts if needed, to make the best decision for your facility’s requirements.
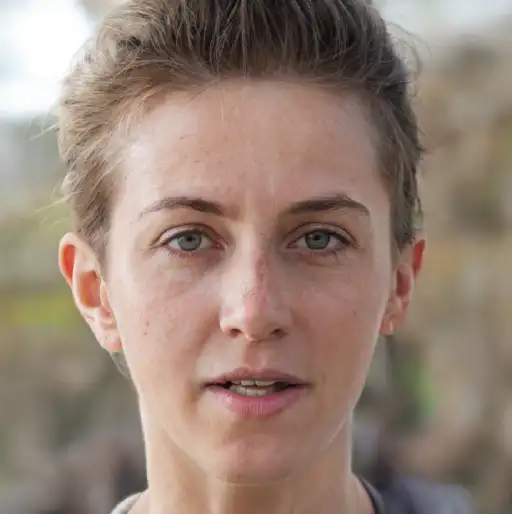
Fran Bullock, a literary explorer rooted in the charm of England, unearths stories that resonate with the echoes of history. With a quill dipped in nostalgia, she pens tales that bridge the past and present, weaving narratives that captivate the soul.