A waste heat fired boiler is a critical component in many industrial processes, recovering heat from exhaust gases to improve efficiency and reduce energy costs. However, proper maintenance and optimization are essential to ensure its longevity, efficiency, and reliability. In this guide, we will explore the best practices for maintaining and optimizing a waste heat fired boiler, covering aspects like routine inspections, cleaning procedures, performance monitoring, and efficiency enhancement techniques.
Importance of Maintenance in Waste Heat Fired Boilers
Maintaining a waste heat fired boiler is crucial to:
- Prevent unexpected breakdowns
- Improve energy efficiency
- Extend the lifespan of the boiler
- Ensure safety and compliance with regulations
- Minimize operational costs
Neglecting maintenance can lead to reduced heat recovery, increased fuel consumption, and costly repairs. Implementing a proactive maintenance strategy helps in avoiding such problems.
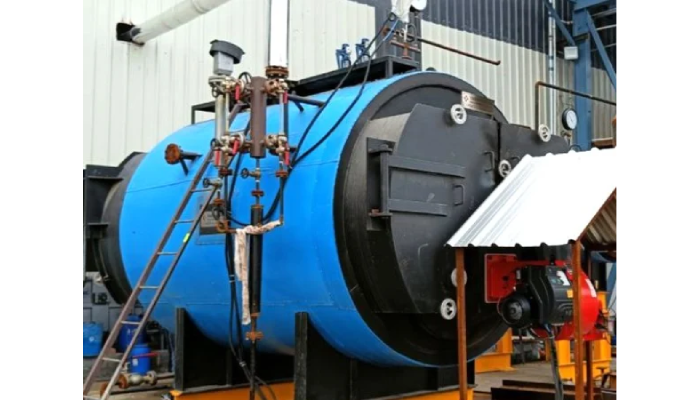
Routine Maintenance Procedures
Regular Inspection and Monitoring
Routine inspections help detect early signs of wear, corrosion, or scaling. Some key areas to monitor include:
- Heat exchanger surfaces for deposits or scaling
- Boiler tubes and refractory materials for cracks and leaks
- Burners and combustion chambers for soot buildup
- Valves and piping for leaks and pressure variations
- Instrumentation and controls for calibration accuracy
Using thermal imaging and ultrasonic testing can help identify potential issues before they become critical.
Cleaning and Descaling
Over time, waste heat boilers accumulate deposits such as soot, ash, and scale, which reduce heat transfer efficiency. Regular cleaning methods include:
- Mechanical cleaning: Using brushes or scrapers to remove deposits
- Chemical cleaning: Using acid or alkaline-based descaling agents
- Soot blowing: Using compressed air or steam to remove soot buildup
Keeping heat exchange surfaces clean ensures optimal heat recovery and prevents overheating issues.
Water Treatment and Boiler Feedwater Quality
Poor water quality can lead to scaling and corrosion, impacting the boiler’s efficiency and longevity. Implementing an effective water treatment program includes:
- Softening the feedwater to prevent scale formation
- Using chemical treatments to control pH and remove impurities
- Regularly testing water quality to maintain optimal conditions
Ensuring proper water treatment reduces maintenance costs and prevents system failures.
Checking and Maintaining the Insulation
Proper insulation reduces heat losses and enhances overall efficiency. Regularly inspect the insulation materials around the boiler, piping, and heat exchangers to:
- Repair damaged or deteriorated insulation
- Prevent unnecessary heat losses
- Reduce energy consumption
Optimization Techniques for Maximum Efficiency
Enhancing Heat Recovery
Maximizing heat recovery is essential for improving boiler performance. Consider these strategies:
- Upgrading heat exchangers to improve heat transfer efficiency
- Using economizers to preheat boiler feedwater
- Integrating additional waste heat recovery units if excess heat is available
By optimizing heat recovery, industries can significantly reduce their energy consumption and operational costs.
Implementing Automated Controls
Modern automation systems help in optimizing boiler performance by:
- Continuously monitoring temperature, pressure, and efficiency parameters
- Adjusting air-fuel ratios for optimal combustion
- Detecting anomalies and triggering maintenance alerts
Upgrading to a smart control system enhances boiler efficiency and ensures consistent performance.
Managing Load and Boiler Operations
Operating the boiler at an optimal load prevents unnecessary wear and improves efficiency. Best practices include:
- Avoiding frequent start-stop cycles, as they lead to thermal stress
- Operating at steady loads to maintain consistent performance
- Using multiple boilers efficiently to match varying load demands
Proper load management ensures that the boiler operates under ideal conditions, minimizing fuel wastage.
Reducing Excess Air in Combustion
Excess air in combustion leads to heat losses and reduced efficiency. By:
- Tuning the air-to-fuel ratio to maintain proper combustion
- Using oxygen trim systems to adjust excess air levels automatically
- Regularly checking for leaks in the air supply system
Industries can optimize combustion efficiency and enhance overall energy savings.
Common Issues and Troubleshooting
Overheating and Tube Failures
Causes:
- Scaling and deposits
- Poor water circulation
- High flue gas temperatures
Solutions:
- Regular descaling and cleaning
- Ensuring proper water treatment
- Monitoring exhaust gas temperatures
Corrosion and Erosion
Causes:
- Poor water quality
- High sulfur content in exhaust gases
- Improper maintenance
Solutions:
- Using corrosion inhibitors
- Maintaining appropriate pH levels in feedwater
- Inspecting and replacing corroded components
Inefficient Heat Recovery
Causes:
- Fouling of heat exchange surfaces
- Poor combustion efficiency
- Unoptimized boiler controls
Solutions:
- Cleaning heat exchangers regularly
- Adjusting fuel and air ratios
- Implementing advanced control systems
Conclusion
Maintaining and optimizing a waste heat fired boiler is essential for maximizing efficiency, reducing operational costs, and ensuring long-term reliability. By implementing a proactive maintenance plan, optimizing heat recovery, and leveraging automation, industries can achieve optimal performance from their waste heat boilers. Regular inspections, cleaning, and water treatment are key to preventing common issues and enhancing overall efficiency. With proper care and optimization, a waste heat fired boiler can provide sustainable energy savings and improved operational performance for years to come.
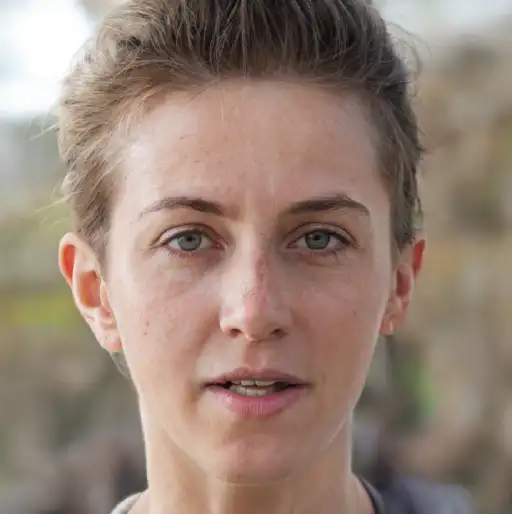
Fran Bullock, a literary explorer rooted in the charm of England, unearths stories that resonate with the echoes of history. With a quill dipped in nostalgia, she pens tales that bridge the past and present, weaving narratives that captivate the soul.